Contact: Robbie Ward
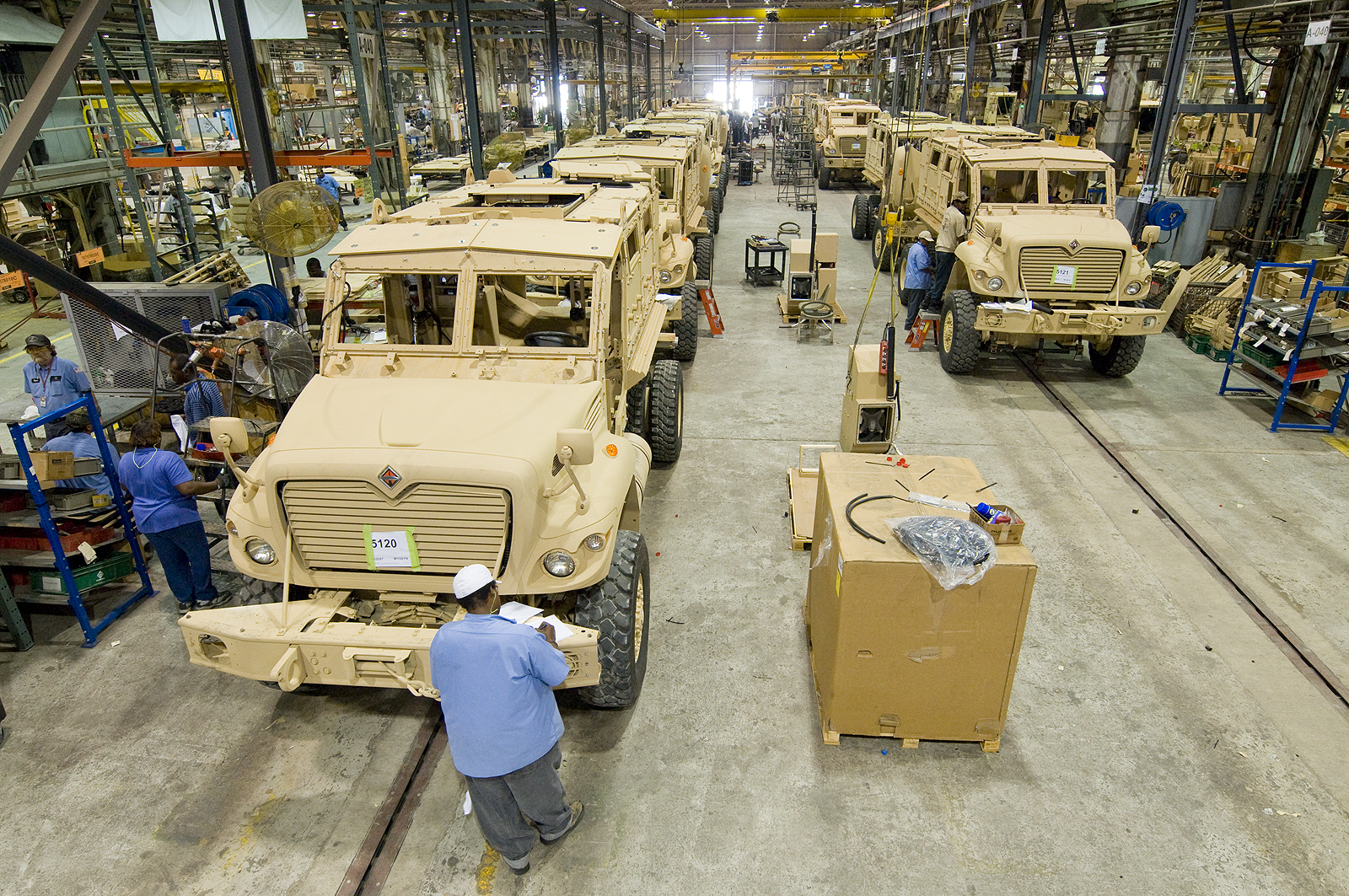
STARKVILLE, Miss.--Dewel Brasher keeps Glenn Dennis' cell phone number on his speed dial.
That sums up the close relationship between a West Point-based military vehicle manufacturer and Mississippi State's Center for Advanced Vehicular Systems Extension.
Brasher, operations manager for the Navistar manufacturing plant in neighboring Clay County, credits Dennis, manager of manufacturing and quality processes, and others at CAVS Extension for helping the international company create and continue to produce high-quality armored vehicles. The university-based engineering resource also is keeping hundreds of jobs in a community struggling with major manufacturing losses in recent years, Brasher observed.
Navistar International LLC recently announced a $752 million contract to supply the U.S. military with armored vehicles. The contract is split between assembly plants in West Point and Garland, Texas.
The current contract is the eighth vehicle assembly project for the hundreds of employees working in West Point. Usually referred to as MRAPs--an acronym for mine-resistant armored protection--the vehicles are credited by the Department of Defense for significant decreases in U.S. soldier deaths in Iraq.
"It would be very difficult to overstate the importance of CAVS," Brasher said. "For one thing, they were able to call on a tremendous amount of resources from Mississippi State, state agencies and other learning institutions. They bring to the table almost anything we want."
To date, CAVS has had an estimated $4.28 billion economic impact on the state. It has helped create or retain 1,600 high-wage jobs, based on client responses to third-party surveys conducted on behalf of the U.S. Department of Commerce's Manufacturing Extension Partnership.
Based in Canton near Nissan's automotive assembly plant, CAVS Extension has partnered with Navistar since 2005, when the company began work on its first armored vehicle in West Point.
From crafting in-depth contract proposals to assisting in the actual manufacturing process, CAVS Extension engineering expertise and sophisticated computer modeling and simulation programs have worked, to date, with more than 50 Mississippi companies.
Glenn Dennis said he and his colleagues feel a special sense of purpose when it comes to work with Navistar.
"When you go into production, you get to see hundreds of people building the trucks on the line and know how appreciative they are to have a good job," Dennis said. "But, the best thing is when you get a picture from the troops in the field sitting on one of the MRAPs made in West Point and know our vehicles have saved numerous lives from attacks."
In 2009, Dennis and Clay Walden, director of CAVS Extension, were honored for their Navistar work with the National Practitioner of the Year Award. The honor was given by the Manufacturing Extension Partnership, a nationwide network of not-for-profit manufacturing assistance centers.
Whether military or civilian in nature, CAVS Extension engineers and staff members focus their efforts primarily in the areas of specific projects with companies and professional development activities, Dennis said.
One recent civilian project was with Hol-Mac, a Bay Springs steel fabrication company.
Charles Holder, the company's founder and owner, credits his partnership for helping increase production by about 15 percent at one Hol-Mac facility. CAVS engineers used modeling and simulation computer programs to determine the most efficient locations to place equipment, parts and related materials, he explained.
"By doing that, we realized there was a lot of wasted motion," Holder said. "It helped us be more competitive."
Holder's business started inside a barn in 1963 with himself and two other employees. Now employing about 400 people, Hol-Mac and CAVS began working together nearly five years ago when company employees began taking professional development classes offered by the extension arm.
Some other CAVS Extension projects around the state include (by location):
CANTON--At the neighboring Nissan facility, CAVS Extension is involved in a series of projects related to the anticipated launch of a new vehicle.
CLEVELAND--Engineers joined with the Mississippi Development Authority and Entergy Corp. for a long-term project to help automotive equipment supplier Faurecia improve a struggling plant. The results: a 35 percent improvement in worker productivity and 80 percent increase in quality.
GULF COAST--Helping the Northrop Grumman shipyard redevelop and modernize its operations after the ravages of Hurricane Katrina.
NATCHEZ--A current project with Bad Boy Enterprises, manufacturer of four-wheel drive electric vehicles marketed to deer hunters.
Walden said CAVS Extension also is continually providing Six Sigma training for employees in a range of state industries. A quality improvement methodology, Six Sigma stresses data-driven problem-solving.
"Everything we do focuses on how to improve quality and productivity," he said.
NEWS EDITORS/DIRECTORS: For more information on the work of CAVS, contact Dr. Walden at 601-407-2713 or walden@cavse.msstate.edu.
For more information about Mississippi State University, see http://www.msstate.edu/.