Contact: Phil Hearn
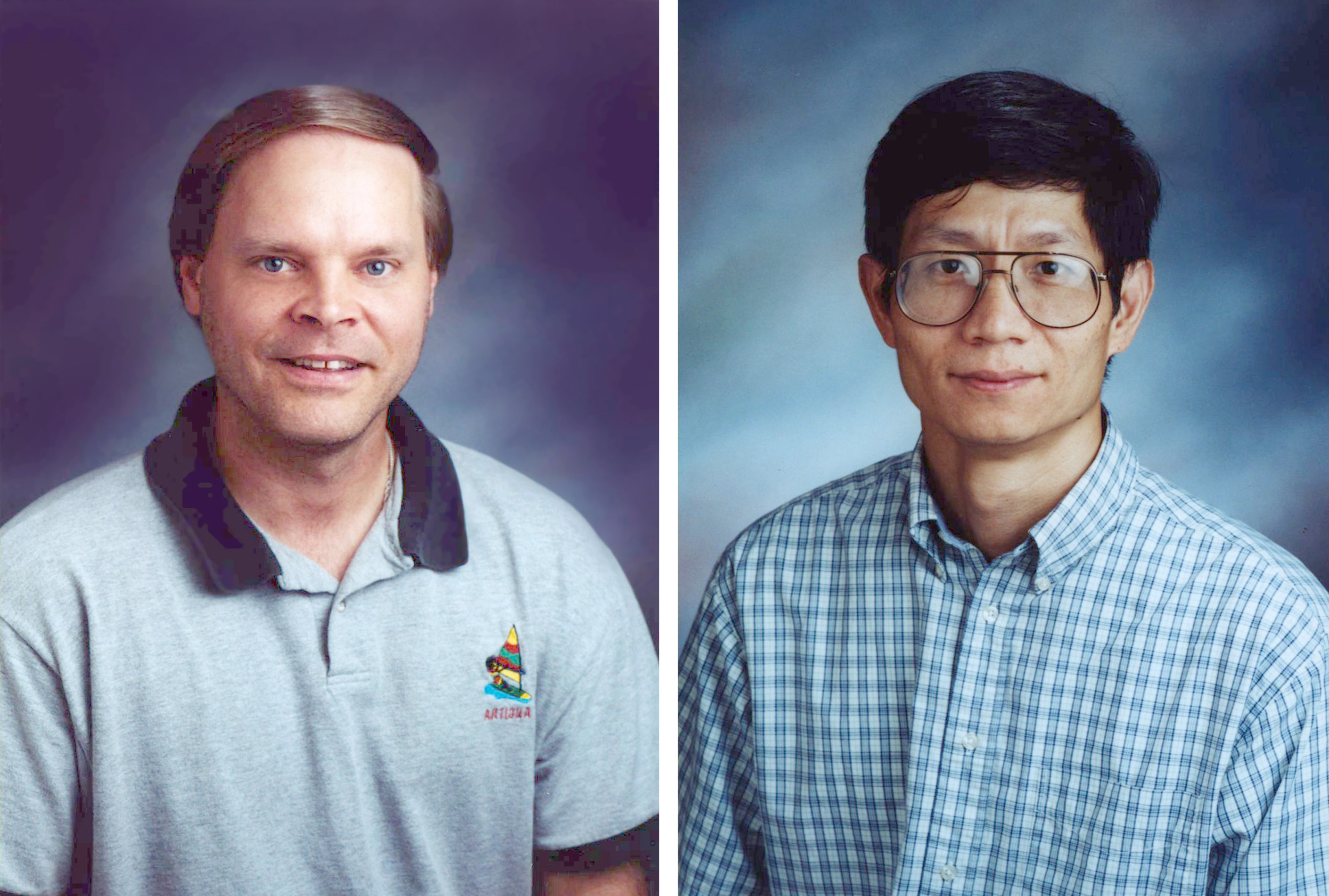
STARKVILLE, Miss.--Two Mississippi State scientists are receiving national recognition from NASA for devising computer software that is saving aircraft engine manufacturers millions of dollars in new engine developments.
Professors Jenping Chen and J. Mark Janus of the university's ERC/Computational Simulation and Design Center won NASA's 2004 Software of the Year Award in their research category while collaborating with the national space agency's Glenn Research Center.
They also received $25,000 for finishing second overall in competition with other category winners representing NASA's Ames, Langley, Marshall, and Stennis research centers, and the Jet Propulsion Laboratory. Overall co-winners were TetrUSS/Langley and Science Activity Planner/NASA Jet Propulsion Lab, neither of which had university collaboration.
"Each center has a different mission," explained David Marcum, the mechanical engineering professor who directs the MSU SimCenter. "Drs. Chen and Janus won their category, then finished as runner-up to the best in show.
"Each award is a national award since all centers use researchers from around the country," added Marcum, noting the SimCenter also conducts different projects with the Glenn, Langley, Marshall, and Stennis centers.
Operating at the ERC (formerly known as the Engineering Research Center), the SimCenter is a research division of MSU's Bagley College of Engineering.
Chen and Janus have been working in collaboration with NASA and private industry over the past 18 years on turbomachinery simulation software. Their research currently is supported under a five-year, $1.5 million contract from NASA's Glenn center; nearly $500,000 from the Army Research Laboratory; and a Department of Defense Challenge Project program for high performance computing resources.
The Chen-led MSU research team was recognized by NASA in the recent national competition for developing TURBO-AE (Turbomachinery Aeroelastic Analysis Code), which is computer software used to simulate the highly complicated flowfield within an aircraft jet engine. Chen is an associate research professor of computational simulation and design, while Janus is an associate professor of aerospace engineering.
"The unsteady flow analysis software TURBO developed at MSU was extended by the development team to analyze the aeroelastic performance of engine components, the result of which has saved aircraft engine manufacturers millions of dollars in new engine developments," NASA officials said in announcing the SOY competition results.
Chen said the TURBO code simulates fluid dynamics in turbomachinery, such as the compressor or turbine of an aircraft jet engine.
"The code provides high fidelity modeling of subsonic and transonic flow regime for aerodynamics and aeroelastic applications," Chen explained. "Millions of partial differential equations that describe the motion of fluid are solved numerically to model the complicated unsteady blade row interaction inside the jet engine, which plays an important role in engine aerodynamic performance that impacts fuel consumption."
Aeroelasticity relates to the elastic properties of structures that are subject to aerodynamic pressures.
"The code also is used in the prediction and control of engine stall, which is detrimental to the engine and should be avoided at all costs," Chen added. "The use of parallel computing--in which hundreds of computers are used in a simulation--has shown that the simulation is now capable of providing results in a time frame that may impact the design process."
Chen said TURBO-AE--jointly developed by NASA, MSU and industry personnel--helps determine blade stability and predict "flutter, the blade vibration that can potentially lead to fatal damage of the engine."
NEWS EDITORS/DIRCTORS: For more information, contact Dr. Chen at
(662) 325-2197 or chen@erc.msstate.edu. Dr. Marcum may be reached at 325-2423 or marcum@erc.msstate.edu.